What is Flexographic Printing? The Basics of Flexo Printing Explained
- Trebnick Systems
- Sep 1, 2022
- 3 min read
Updated: Jun 10, 2024
At Trebnick, we primarily print our products via flexographic printing or flexo for short. Using a flexo press, we can utilize up to 16 different ink colors and print on a variety of materials. But what exactly is flexo printing, and how does it compare to other printing methods?
How Does it Work?
Flexographic printing involves using flexible relief plates to transfer liquid ink to the material to print text and graphics. The thing that sets flexo apart from other printing methods is its compatibility with different materials and inks. Materials that would be difficult to print on for other printing methods are easy for flexo. Additional processes, such as laminating, embossing, cold foil stamping, and die-cutting, can be integrated into the printing process on a flexo press. Completing everything in a single pass greatly increases efficiency and production speeds, which results in a lower cost to our customers.

The starting material comes in rolls and is passed through a series of rollers and cylinders of various sizes. A typical flexo press uses four roller types: a metering roller, an anilox roller, a plate cylinder, and the impression cylinder. The metering roller takes the ink from an ink tray to an anilox roller, which controls how much ink is transferred to the plate cylinder. A flexible printing plate is mounted to the plate cylinder and is used to apply the ink to the material as it passes between the plate cylinder and the impression cylinder, using pressure to transfer the ink from the plate to the material.
Substrates and Materials
Flexo presses can print on a variety of materials such as uncoated papers, coated papers, carton boards, liner boards, aluminum foil, and plastic films. They can also print on non-woven fabrics and different types of laminates. This flexibility makes flexo printing perfect for self-adhesive labels, industrial tags, food packaging, plastic bags, and flexible packaging. Check out a list of some of our printable materials on our website!
Plates and Ink
Flexo presses print directly from plate to paper. Flexible relief plates are made of a photopolymer material and form a reversed impression of a design. The inked plate has a raised image and rotates at high speeds to transfer the ink through small holes and lays it down on the material. Each color requires a different plate, so if there are four colors on the design, for example, there will need to be four ink stations, four of the same size cylinders, and four corresponding plates for each separation. Some designs may involve multiple shades of the same color, such as black and gray. In that case, a plate will contain all of these shades using screens. Screens on a plate can produce different tints of one ink color. Keep in mind that depending on your design, and how accurate the color needs to be, it may still require its own plate to print.

Flexo printing also provides the flexibility to use various types of inks. UV inks are cured with ultraviolet light, rather than standard drying methods used for water- or solvent-based inks, allowing them to dry faster. UV ink is perfect for any tags or labels that will be left out in the sun, as the UV light from the sun cures the ink further. Various clear varnishes or metallic inks can also be applied to customize the final printed product!

Dies and Perfs
Dies and perfs are what give a tag or label its size and shape. Dies function almost exactly as a plate does. The die rolls over the material, but instead of printing a design, it cuts a pattern, separating labels or tags and giving them their shape. Holes and C-punches get punched out, and perfs are added right before the finished product comes off the press. There are Solid Dies, which are integrated into a cylinder and then mounted onto the press, and Flex Dies, which work like a plate and get wrapped around a cylinder.

Advantages to Flexographic Printing
- Runs at extremely high speeds (up to 2000 ft. per minute) and is ideally suited for long printing runs.
- Prints on a wide variety of substrate materials.
- Short set-up times with a minimum of waste; guarantee high-quality output.
- Eliminates the need for additional work and cost: printing, varnishing, laminating, and die-cutting can be done in a single pass.
Disadvantages to Flexographic Printing
Flexography vs. Offset
Flexography vs. Lithography
Trebnick Systems specializes in flexographic printing. Our newest state-of-the-art press introduces RFID and integrated labels into our expansive list of capabilities. Contact us today to see what solutions we can provide to your printing needs!
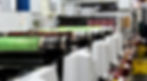